Abstract : This paper designs an intelligent tracking car based on the inclusive structure. The car uses the AT89S51 microcontroller as the controller. The system mainly has obstacle avoidance behavior module, trajectory tracking behavior module, remote control behavior and emergency stop module. The infrared sensor is used to design and detect the trajectory module, and the ultrasonic sensor is designed to avoid the obstacle module. For the obstacle avoidance behavior module, a fuzzy control algorithm is proposed to avoid obstacles. A lot of experiments have verified that the car can not only track the trajectory stably, but also walk around obstacles.
This article refers to the address: http://
Smart car is a comprehensive system integrating environment sensing, dynamic decision-making and planning, behavior control and execution. It is a simplified mobile robot that is widely used in smart vacuum cleaners, handling small objects, cleaning garbage, etc. . The so-called intelligence, that is, without the human intervention, can automatically complete the given task. However, the environment is unknown, the task is complex, and a single sensor cannot realize its function. Multi-sensor information technology is used to perceive the surrounding environment and task execution is an effective measure. Through comprehensive judgment processing of multi-sensor information, the environment is obtained. Correct understanding makes the car system fault-tolerant and ensures the rapidity and correctness of the system information, which is more reliable than the single sensor can achieve. The architecture of commonly used robots has a layered architecture, an inclusive architecture, and a hybrid architecture. In the 1980s, Brooks proposed the behavioral and inclusive structure of robots, breaking down complex tasks into simple units that can be executed concurrently. Each unit has its own perceptron and actuator. Multiple behaviors are coupled to form a hierarchical model, with emphasis on linkages between different layers and distribution of different behavioral functions. The smart car is also a simplified mobile robot whose motion control is to move the smart car along the desired path by adjusting the speed and direction of movement of the smart car. The behavior of robots can be divided into two categories: reactive and deliberate. Reactive behavior is an incentive-response behavior that does not require a computational process and has a short response time. The inclusive structure proposed by Brook et al. is a typical reaction paradigm. The behavior is layered according to the level of ability. The higher level behavior can cover the adjacent low-level behavior output. Deliberate behavior is a learnable, conscious act. It is to add planning to the reaction, so that the robot has the ability to remember and reason. Traditional methods based on perceptual-modeling-planning-action are not easy to establish accurate environmental models, and it is difficult to achieve path tracking in dynamic and unknown environments. The reaction is a direct mapping from perception to action, and the smart car can respond quickly to the external environment. Based on the research purpose of this paper, designing an intelligent tracking car in an unknown and dynamic indoor environment requires not only stable and real-time tracking of a given trajectory movement, but also the tracking process automatically bypassing obstacles, using a track based on the inclusive structure. The line tracking control method is designed to design an intelligent tracking car.
1 Intelligent tracking car design principle
The intelligent tracking trolley can walk along a given route in an environment without human intervention and can bypass obstacles or emergency stop when suddenly obstacles appear. The designed car mainly realizes intelligent tracking. The single-chip AT89S51 is used as the controller. The reflective infrared photoelectric sensor is used to detect the guiding trajectory of the road surface. The piezoelectric ultrasonic sensor is used to realize the intelligent obstacle avoidance of the trolley. With NT- The T10A transmitting module and the XY-R04A receiving module are used as wireless remote control modules to realize remote control of the smart car. At the same time, the operating state and speed of the car are displayed on the LCD screen. The two DC motors are each one of the left and right wheels, using L298N. The two DC motors that drive the electric car realize the straight and turning of the trolley. The main implementation hardware structure of the system is shown in Figure 1.
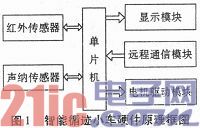
The main task of the smart car realizes trajectory tracking. Firstly, the road information is obtained according to the infrared sensor, the tracking trajectory is detected, and the obtained trajectory information is used for calculation to determine whether to drive the left or right wheel, turn the angle to the left or right, and start the obstacle avoidance. Function, detect whether there is any obstacle, if there is, end the trajectory tracking and perform obstacle avoidance. Determine whether there is a remote human control command, and if so, end the trajectory tracking or obstacle avoidance function and respond to the remote control command. Also check if there is an end program command, and if so, end all tasks. The basic behavior module of the system is shown in Figure 2. The horizontal decomposition task structure mode is adopted, and each behavior is running, which is realized by the interrupt setting of the single chip microcomputer.
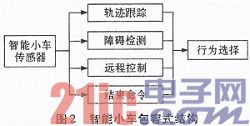
2 behavior module design
2.1 Obstacle avoidance module design
Two ultrasonic sensors are used, which are designed on the left and right sides of the trolley. Figure 3 shows the left ultrasonic sensor connected to the microcontroller. VCC is connected to 5 V power supply, Trig is connected with P1.0 of AT89S51 single-chip microcomputer, Echo is connected with AT89S51 single-chip microcomputer P1.1, and GND is connected with ground. The connection of the right sensor is the same as that on the left side, but the connection to the MCU is P1.2 and P1.3 respectively.
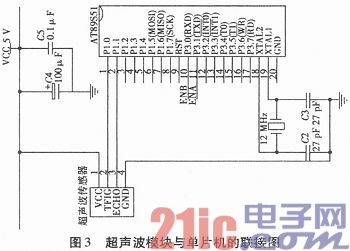
The obstacle distance information is obtained by multiplying the time interval of the ultrasonic wave from the transmitted sound wave to the reflected sound wave. Let the time interval be t, and the propagation speed of the ultrasonic wave in the air is v, then the distance d between the sensor and the obstacle is:

Obstacle avoidance not only enables the smart car to perform its tasks smoothly, but also prevents the smart car from damaging the environment. At present, there are many methods for mobile robots to avoid obstacles. In terms of research on known environmental information, there are mainly vector force field method, grid method, artificial neural network method, simulated annealing algorithm and ant algorithm. For the obstacle avoidance research with unknown environment, there are artificial potential field method, fuzzy logic method, etc. The fuzzy logic method combines the robustness of fuzzy control itself with the physiological-based “perceptual-action†behavior, which is a mobile robot in complex environment. The obstacle avoidance navigation in the middle of the new ideas. The fuzzy logic method avoids the characteristics of relying on environmental information and has strong superiority in dealing with unknown and real-time complex environments. For obstacle avoidance, the fuzzy control algorithm is used to avoid obstacles. The distance between the smart car and the left and right obstacles is divided into three semantic variables, namely large, medium and small. The output speed is also divided into three semantic variables. The medium and slow designs use PWM waves to control the motor speed, and the fuzzy controller output directly controls the pulse width.
2.2 Trajectory tracking module
The system has designed three infrared sensors, which are placed in the left, middle and right directions of the electric vehicle to read the black trajectory on the ground. When the driving direction deviates from the trajectory, the direction of the deviation of the driving can be judged by the three infrared sensing devices, and the real-time information is transmitted back to the single-chip microcomputer in a high-low level manner, and then the corresponding DC chip can be controlled by the processing of the single-chip microcomputer. Correct the driving route and finally complete the task of automatic tracing. The working process of the infrared sensor is as follows: When the driving direction deviates from the trajectory to the right, two situations occur: 1) the middle and left infrared sensors simultaneously touch the ground black line, and the right sensor touches the white ground; 2) left One sensor on the side touches the black line, and the middle and right sensors touch the white part of the ground. In both cases, the driving direction is shifted to the right. There are two cases when a similar car has a left offset. These three sensors are input as the input signal of the driving data from the I/O port of the single chip microcomputer, then a voltage of TFL is needed, and the sensitivity of the sensor can be finely adjusted according to requirements to meet the sensitivity requirement. Therefore, these three signals can be introduced into the voltage comparator composed of LM324 for level shaping, and finally used by the single chip microcomputer.
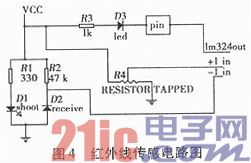
Figure 4 is a schematic diagram of an infrared light sensor circuit. VCC is connected to the 5 V power supply. D1 is an infrared emission tube. It is connected to a current limiting protection resistor R1. D2 is an infrared receiving tube and is connected with a pull-up resistor. When the white ground is touched, the infrared light is reflected back to the receiving tube, and the receiving tube is turned on. This sensor outputs a low level signal to the inverting port of the LM324. At this time, a high level signal is drawn from the varistor. For the same port of the LM324, then after the comparison of the LM324, a high level signal is output to the pin header, and the cathode of the LED in series with the pin header is LM324 which is not able to conduct and cannot emit light. If the sensor is exposed to a black wire, the infrared light is absorbed, and the receiving diode is turned off. At this time, the sensor outputs a high level to the inverting port of the LM324, and the level of the LM324 co-directional port has no high inverting port. The LM324 outputs a low level to the pin header, and the LED connected in series with the pin header turns on, indicating that the sensor is touching the black wire. According to the detection results of the left, middle and right infrared sensors, the motor speed is sent to the single-chip microcomputer after LM324 shaping, and the single-chip microcomputer outputs different PWM waves to control the rotational speed of the left and right wheel motors.
3 behavior control module design
As a hybrid system, behavior-based systems must not only control the continuous dynamic behavior of smart cars, but also systematically and strategically face sudden random events (such as obstacles in the environment). The first issue is how to design a variety of possible effective behaviors, and secondly how to effectively coordinate or fuse conflicts or competition between different types of behaviors to achieve a satisfactory result. In order to be able to achieve multiple goals at the same time, sometimes the smart car needs to perform multiple basic actions. Only one behavior is triggered at a time, and the system generally runs smoothly. However, what should a smart car do when two or more actions are triggered at the same time, and each action requires a smart car to perform different operations?
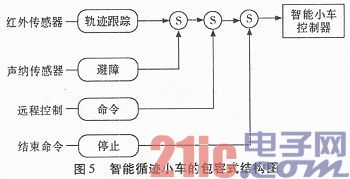
In order to solve the real-time problem of the smart car, the design chooses the inclusive structure for task decision. The inclusive structure decomposes the complex trajectory tracking task into several sub-tasks in the horizontal direction. Each sub-task functional layer has the function of independently completing the task. The high-level functional layer suppresses the lower-level functional layer. As shown in FIG. 5, the trajectory tracking system layer is a high-level functional layer. According to the behavior control method, the priority of the functional layer is first determined, and the lower the functional layer, the higher the priority. As shown in Figure 5, the function layer end command is the lowest, but the priority is the highest. When the end command needs to be executed during the motion, the car performs one of the other three functions, first responding to the end command, and the trajectory tracking function layer is the lowest. At the time of the obstacle, the smart car first performs obstacle avoidance and then performs trajectory tracking. There are 4 functional layers in this design:
1) need to stop running the program in case of emergency behavior;
2) remote control behavior;
3) Obstacle avoidance behavior;
4) Trajectory tracking behavior.
According to the behavior control method, the priority of the functional layer is first determined. The lower the functional layer is, the higher the priority is, that is, the Leve10 has the highest priority. In the event of an unexpected situation, the human can end the process by ending the program running. Artificial remote control as the first layer can achieve the operator's wishes. When you suddenly encounter an obstacle, avoid the obstacle as the second layer, and bypass the obstacle during the tracking process before continuing to track.
The trajectory tracking behavior generated by the infrared sensor is set to the highest level, because the smart car and the person's safety are the first in the tracking process, so its priority is the lowest. The S in the circle in Fig. 5 means “suppressâ€, that is, the high-priority behavior suppresses the low-priority behavior control. When there is a sudden obstacle in the trajectory tracking process, the smart car first starts the obstacle avoidance behavior and pauses the tracking. Behavior, the obstacle avoidance behavior ends the immediate execution of tracking behavior.
4 Analysis of experimental results
The designed tracking car has a good tracking effect, and trajectory tracking experiments are performed on the ground and white paper respectively. The trolley tracking track is shown in Figure 6. For the intelligent tracking car designed in this paper, not only the straight line can track stably, even the irregularly curved line can track well.
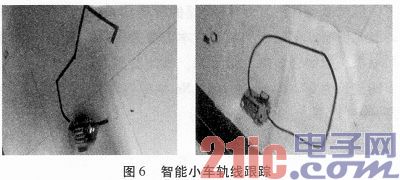
Since the blind walk procedure for anti-interference is set in the software. Therefore, the anti-jamming performance of the system can be verified by using an error track and uneven bend test with uneven track lines. After testing, when the trajectory of the road surface is not uniform, the car can blindly follow the previous state command, and can pass the trajectory line segment with uneven trajectory. The program of in-situ rotation is set in the car block. In theory, the car can pass a corner close to 180 degrees. Therefore, the car has a certain cornering performance. After testing, the car can pass at the corner. However, due to the uneven control of the driving speed of the trolley, there is a certain probability that the straight line and the curved contact section will rush out of the runway.
When the car is in an accidental state during the tracking process, that is, when an obstacle is suddenly encountered, the car can walk along the obstacle until the track is in front of the track without obstacles. When the obstacle is close enough or in a closed small range, the car may sometimes turn right and turn right when it is too straight, causing the car to keep turning right in this range, and at the same time detecting no obstacles. When the trajectory is used, it indicates that the trajectory tracking of the trolley fails, the program ends automatically, and the trolley stops.
5 Conclusion
In this paper, an intelligent tracking vehicle based on inclusive behavior control is designed. The single-chip AT89S51 is used as the controller. The infrared sensor detects the trajectory, and the detection result is transmitted to the single-chip microcomputer through LM324 shaping. The design program outputs the suitable PWM wave control smart car. Left and right wheel speed. The ultrasonic sensor detects the obstacle information, designs the fuzzy obstacle avoidance controller, and uses the controller output result for the motor speed control, so that the smart car realizes automatic obstacle avoidance and walks around the obstacle. A lot of experiments have been done indoors and outdoors. The car designed in this paper not only can track the black trajectory stably, but also can walk around obstacles when encountering obstacles.
Metal Sign Post, Street Sign Post, Traffic Sign Post, Steel Sign Post
YIXING FUTAO METAL STRUCTURAL UNIT CO.,LTD( YIXING HONGSHENGYUAN ELECTRIC POWER FACILITIES CO.,LTD.) , https://www.chinasteelpole.com