Mentor Graphics recently released a research report titled "Improving the Competitiveness and Reliability of Automotive Products - The Importance of Thermal Management in Automotive Electronics Design."
This article refers to the address: http://
1. Report author introduction
John Isaac, Director of Market Development at Mentor Graphics.
2. Preface, background
The electronic functions in today's cars (Figure 1) continue to increase and will soon outweigh the value provided by mechanical functions. Electronic functions are also becoming the main competitive element of the model. The constraints of on-time delivery of models are no longer mechanical, but electronics and software. Therefore, it is necessary not only to quickly design these electronic components, but also to have high performance, quality and reliability standards. If they are less reliable and fail after the sale, the company will not only suffer huge warranty and recall costs, but also damage its reputation.
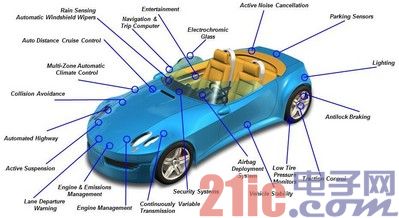
Figure 1 -- Electronic features in today's cars continue to increase
The main source of heat for electronic devices is their semiconductor chips (ICs), which are very temperature sensitive, making the design of cooling solutions a challenge. Overheating can cause the chip to fail prematurely. With the increase of functions, the related heat dissipation problem has become increasingly prominent, which has become a potential constraint factor in the development of electronic devices. For critical components, a proper cooling strategy is needed to prevent overheating and failure.
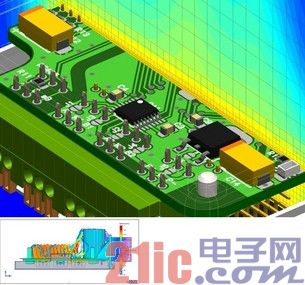
Figure 2 -- All automotive electronics, including electronic control units (ECUs) and pump controllers, require good thermal management
3. The main points and outline of the full text are as follows:
Why start with the conceptual design phase?
By using Mentor Graphics' new FloTHERM XT solution, mechanical designers or thermal design engineers can easily create conceptual models of ICs, PCBs, and chassis, and then simulate to see if they can dissipate heat efficiently. If you can, then from a thermal management perspective, the design can go on. If the personnel of any other design department find it impossible to proceed after the concept phase, they may need to change the system's functional specifications, size specifications, devices used, or other factors. However, if problems are discovered and redesigned in the subsequent development process, the cost will increase significantly.
Another reason to consider thermal design from the conceptual stage of the development process is to provide guidance for subsequent detailed design. Before detailed design of a PCB or chassis, designers can easily create and compare multiple conceptual designs, then select the best solution and use that data to guide detailed system design.
Designing automotive components with FloTHERM XT
Figure 3 shows a typical flow for designing complex parts using FloTHERM XT. The first step in the process is the conceptual layout of the PCB. In this step, the designer can make a rough model of the PCB board and the components he/she knows will generate heat. When you use the tool, you can create your own component models or pick models from the SmartPartsTM library. The SmartParts library contains a complete component model and a template that can be easily modified into the actual component structure. These components can then be positioned on the conceptual design PCB.
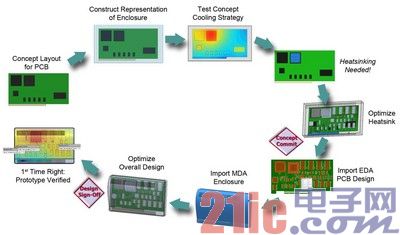
Figure 3 - Using FloTHERM XT, the design process from concept to final solution validation is closely integrated with MDA and EDA design tools.
The designer can then create a conceptual design chassis and place the PCB in the chassis. FloTHERM XT has a complete mechanical design capability, so the components or chassis models can be refined as needed to properly describe the target product. Once the PCB is placed in the chassis, boundary conditions can be added and CFD thermal simulation analysis can be performed. The designer can modify the component layout based on the results, add heat sinks to the overheated components, modify the chassis, and then re-analyze.
Continue the process until the designer is satisfied (he/she has a good thermal management solution). The heat related components are placed correctly on the PCB. The PCB board is placed correctly in the chassis. The chassis shape and materials provide good conduction, convection or heat radiation. Then, you can end the conceptual design work and pass the information to the MDA and EDA designers for detailed design.
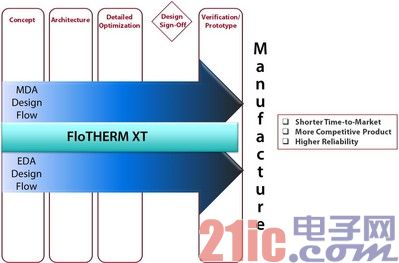
Figure 4 -- A fast and accurate thermal analysis tool (combined with MDA and EDA) that can be used by both designers and thermal professionals can help meet the aggressive business needs of automotive companies.
4. Summary of the research report
With FloTHERM XT, design engineers can perform front-end analysis, grasp trends, solve problems quickly, and achieve greater project progress by quickly solving and comparing different scenarios, effectively complementing the work of full-time analysts in the post-project validation phase. The simulation cycle time can be reduced from weeks to days or days compared to traditional CFD software. Designers can compare a variety of designs to develop more competitive and reliable products, while shorter simulation cycle times can speed time to market (Figure 4).
24v power supply, the current range is 2A-9.2A, the max power is 220w. We also can meet your specific requirement of the prodcuts.The material of this product is PC+ABS. All condition of our product is 100% brand new.
Our products built with input/output overvoltage protection, input/output overcurrent protection, over temperature protection, over power protection and short circuit protection. You can send more details of this product, so that we can offer best service to you!
24V Power Supply,24V Pc Power Supply,24V Dc Power Supply ,24V Power Supply For Pc
Shenzhen Waweis Technology Co., Ltd. , https://www.huaweishiadapter.com