First, the concept of fieldbus control system (FCS)
Fieldbus control is a computer local area network for industrial equipment automation control. It relies on a micro-processing chip with detection, control, and communication capabilities. The digital instrument (device) realizes complete decentralized control in the field, and uses these on-site scattered measurements to control a single point of the device as a network node, and these points are connected by bus. Get up and form a fieldbus control system. It belongs to the lowest-level network system and is a network-integrated fully distributed control system. It distributes the functions of the original distributed dcs system field controllers at various network nodes. To this end, the original closed, dedicated system can be turned into an open, standard system. The products of different manufacturers can be interconnected, which is the replacement of DCS system, which greatly simplifies the system structure, reduces the cost, better meets the practical requirements, and improves the reliability of the system operation. The fieldbus control system of different communication protocols is generally connected to the fieldbus network segment through the PC interface board of the bus slot in the industrial PC. The figure shows a fieldbus system with a PC1 interface card. Each interface board can have 4 bus segments. For the system to be reliable and secure, two identical PCs are redundantly set up. In the figure, plc is a program controller for switching system switching control.
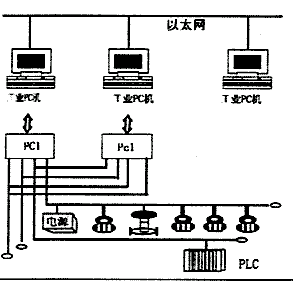
Second, the composition of the fieldbus control system
The fieldbus control system consists of three parts: measurement system, control system and management system. The hardware and software of the communication part is its most distinctive part.
1. Fieldbus control system:
Its software is an important part of the system. The software of the control system includes configuration software, maintenance software, simulation software, equipment software and monitoring software. First choose to develop the configuration software, control the operating human interface software MMI. Through the configuration software, the connection between the function blocks is completed, the function block parameters are selected, and the network configuration is performed. Data is collected, processed, and calculated in real time during the network operation. Optimize control and logic to control alarms, monitors, displays, reports, and more.
2. Fieldbus measurement system:
It is characterized by multi-variable high-performance measurement, which makes the measuring instrument have more functions such as computing power. Because of the digital signal, it has high resolution, high accuracy, anti-interference and anti-distortion ability, and also has the status of instrumentation equipment. Information, you can adjust the process.
3. Equipment management system:
It can provide diagnostic information, management information, equipment operating status information (including smart meters) and equipment manufacturing information provided by the manufacturer. For example, Fisher-Rosemoune Company, launched the AMS management system, which is installed in the host computer, and completes the management function, which can form a comprehensive management system information base of the field device, on which the reliability analysis and predictability of the device are realized. maintain. Changing the passive management mode to predictable management and maintenance mode The AMS software is a T-type structure based on the field server. It supports modularization on the field server, and the function-rich application software provides users with a graphical interface.
4, bus system computer service mode:
The client/server model is currently the more popular network computer service model. The server represents the data source (provider) and the application client represents the data consumer, which takes the data from the data source and processes it further. The room machine runs on a PC or workstation. The server runs on a minicomputer or mainframe, and it uses both intelligence, resources, and data to complete the task.
5, the database:
It can organize and dynamically store a large amount of data and applications, achieve full sharing and cross-access of data, and is highly independent. The parameters of industrial equipment change continuously during operation, the amount of data is large, and the real-time requirements of operation and control are very high. Therefore, a database system that can communicate with each other and real-time performance is formed. The market is mature, such as Orad, sybas, Informix, SQL Server in relational database; Infoplus, PI, ONSPEC, etc. in real-time database. .
6. Hardware and software of the network system:
The network system hardware includes: system management host, server, gateway, protocol converter, hub, user computer, etc. and the underlying intelligent instrument. The network system software has network operation software such as: NetWarc, LAN Mangger, Vines, server operation software such as Lenix, os/2, Window NT. Application software database, communication protocol, network management protocol, etc.
Third, the characteristics of the fieldbus control system
1. In the function management, the control is dispersed, and the structure is horizontally dispersed and vertically classified.
2, to have fast real-time response capability, for the industrial equipment's local area network, its main traffic is process information and operation management information, the amount of information is not large, the transmission rate is not high below 1MPS, the information transmission task is relatively simple but in fact The time response time requirement is higher from 0.01 to 0.5S. The so-called real-time is the parameter that can collect the process in real time in the process of network communication, process the system information in real time, and quickly feed back to the system to complete the process control to meet the time limit requirements of process control. In addition to controlling the external devices of the computer system, it also controls the devices that manage the control system and has the ability to handle random events. The actual operating system should ensure timely disposal under abnormal conditions, ensure the completion of tasks, or complete the most important tasks, require timely detection of corrective random errors, at least ensure that the impact of errors is not expanded, and should have resistance to erroneous operations and incorrect input of information. ability. The main measures to achieve real-time performance of the fieldbus control system are:
(1) The 7th layer of the OSI protocol provides a high degree of functional services, which reduces communication traffic and increases transmission time, thus affecting real-time response capabilities. Therefore, the OSI seven-layer communication protocol is simplified to varying degrees, reducing the complexity of inter-layer conversion and affecting the real-time response capability. The communication protocol of the fieldbus control system is generally the physical layer, the link layer, and the application layer, and then one user is added as a network node to be interconnected into an underlying bus network. Such as the four-layer structure of the PRUFIBUS total layer.
(2)) Put the basic control function into the field with intelligent chips or function blocks, so that the control functions are completely dispersed, directly facing the object, and the interface is intuitive and simple. The function blocks with control, measurement and communication functions, and the function block application process, as network nodes, are interconnected into the underlying bus network. For example, in the PRUFIBUS bus system, the underlying communication and control are concentrated in the slave station according to the master station and the slave station. Each company's manufacturers provide a complete range of main and slave serial chips, which is simple and inexpensive to implement. Like LONWORKS, although the communication protocol is the same as OSI, it is seven layers, but all are solidified in a core chip. It does not need to be transmitted over the network. It can also speed up real-time response. At the same time, the application defines a special object network variable that exists in the neuron chip. In ROM, it is determined when the node code is compiled and will be different nodes. The same type of network variables are connected and controlled, which greatly simplifies the process of developing and installing distributed systems.
(3) Medium access protocol: Generally, the token transfer bus access mode (TOKEN BUS) can achieve the purpose of fast communication and high cost performance. For the multi-access collision detection (CSMA/CD) method, although communication The management is relatively simple, but the collision phenomenon cannot be completely avoided, and the conflict detection is complicated. In addition, the normal interference and errors in the line are often difficult to distinguish from the collision. Therefore, the real-time requirements of the fieldbus control system are not very high. Suitable for. So most bus control systems are token pass access. Only LONWORKS is improved, that is, CSMA access with predictive P. When a node needs to send information, it first predicts whether the network is idle, if it is idle, it sends it, and if it is not idle, it does not send it temporarily, thus avoiding the collision and reducing the network collision rate and improving the efficiency at the time of heavy load. An emergency priority mechanism has been adopted to improve its real-time and reliability.
(4) Communication mode: Generally, the scheduled dispatch communication and the non-scheduled communication are mostly scheduled communication, which are used for periodic transmission between devices, and the control data is preset. Non-scheduled communication is used for parameter setting and device diagnostic alarm processing. From its function, there is a distinction between the primary station and the secondary station. The slave only acknowledges when it receives the message or sends a message to the master when it makes a request, so only a small part of the bus protocol is economical and real-time.
3, the product must be interoperable
Each manufacturer's products shall pass the OSI standard one-time test and interoperability test according to the various bus system protocols, and be certified by a special test center. In order to improve its reliability, it is also subjected to robust testing in harsh environments. The interface technology adopts the OEM integration method to form a product, which can realize open data transmission.
Therefore, different manufacturers' products for the same type of protocol can be mixed and configured as an open system, making it interoperable.
4. Require high reliability measures:
(1) The hardware has been carefully selected using dedicated chip (ASIC) and surface mount technology (SMT).
(2) The system software selects simple and easy-to-use software that is suitable for practical needs, and good tool software. The application software adopts functional modular design and the definition is clear and clear.
(3) It can quickly eliminate faults through online, and enhance hardware repairability, such as I/O template can be plugged in and out, and the fault display is diagnosed, and the components are automatically isolated during faults.
(4) Software separation architecture and each process station have geographically independent local databases. And a global database is logically formed through the communication network.
(5) There are multiple levels of security measures, using fault-tolerant technology and redundancy technology.
Data Cable, HDMI Cable, USB Cable for TV and Computer
Data Cable, HDMI Cable, USB Cable
Ningbo Multitasking Electronic Co.,Ltd , https://www.smartmultesic.com