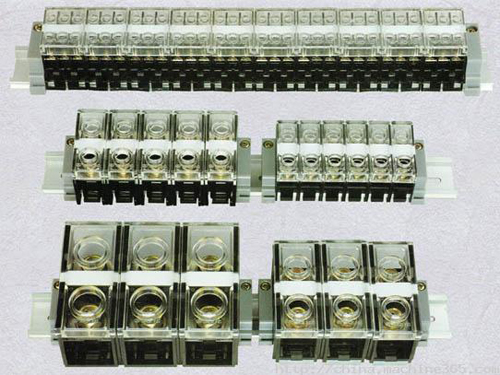
The terminal block is an important accessory product for connecting, from the system, sub-system, combination, printed board to each replaceable individual unit, responsible for the control system's power transmission and signal control and transmission. So this determines the application of the terminal is ubiquitous, as long as the need for wiring will have a terminal.
Terminal implementation standards:
Due to the importance of the terminals, the terminals must meet safety and environmental protection standards when they are designed and used. Only by meeting the standards can we buy the rest assured and use the peace of mind to avoid the hidden dangers of security accidents. Manufacturers of general terminal blocks perform mechanical and electrical components of the device when designing the finalized product.
Terminal products in their field of innovation:
1. Insulation material material nylon (PA66), flame retardant grade V0, does not contain any harmful halogens at the same time, superior flame retardant performance, safety, and environmental protection. Other commonly used materials are thermoplastic polyesters (PBT); and liquid crystal polymers (LCP) that are used in conjunction with perforated reflow technology.
2. Screw terminal:
Terminals for screw connections have always played an important role in the electronics industry and have now become an important component of printed circuit boards. Its structured design takes into account the features of convenient wiring and reliable screw connections.
3. Spring connection terminal:
The spring-connected printed circuit board terminals are divided into two types: pull spring connection and butterfly spring connection. The pull-back spring terminal and the screw terminal can be mutually compatible, which greatly increases the flexibility. Reliable connection: Front connection, obvious connection, low maintenance, no need to tighten.
4. IDC quick strip terminal:
The IDC strip-free quick-connect terminal allows quick connection to insulated conductors without the use of any tools. Pull the booster lever to push the wire into the knife edge and cut off the insulation to achieve an airtight connection. This wiring method saves wiring time by up to 60%, does not require wire stripping, does not require tools, and only requires wire breaks, and nothing more. Also certified for Ethernet cabling (Cat 5).
Regardless of the connection terminal, they all have the following advantages:
1. Large wiring capacity, can adapt to various wiring requirements.
2. The clamping frame is mechanically decoupled from the welding pin, ie because the clamping frame is not integrated with the welding pin, the torque when tightening the screw will not be transmitted to the welding point.
3. The solder pin has a four-cornered shape and the end shrinks. When inserting the solder hole, the contact area is increased. Solder solution is easily dissolved into the solder hole and is not easily soldered.
4. The solder pin is a copper alloy and the solder pin has no dirt to ensure the long-term reliability of the solder.
5. Tinned solder pins for easy soldering.
6. With cooling channels.
7. The tip of the solder pin shrinks and is easy to install.
Users can not only choose different parameters according to their needs, such as needle position and needle distance, but also can choose different wiring directions. In practical applications, the layout of the components (such as the position in the housing) often limits the wiring of the printed wiring board terminals. Printed circuit board terminals that provide a variety of different wiring orientations are undoubtedly of practical importance: horizontal, vertical, oblique, and frontal. The more choices offered, the more helpful the actual operation.
Printed circuit board terminals can even provide multi-layer wiring (1 to 4 layers) terminals. The arrangement between the layers is very compact and staggers in the vertical direction by half a stitch. This terminal perfectly meets the compact, space-saving design needs of the layout.
The screw connection can be compatible with spring connection terminals. The so-called compatibility means that both can be interchanged without changing the layout of the printed circuit board. This greatly improves the product's adaptability and reduces costs to a large extent.
In order to meet the requirements of the new electronic assembly process, the new technology of perforated plug-in reflow was introduced.
It has the following advantages:
1. Elimination of local immersion brazing or press-in.
2. Fully compatible with surface packaging technology.
3. Can be fully integrated into the automated installation process.
4. There is no need for additional space in the production hall.
5. Usually no additional investment costs are required.
HOMBO Technology Public Limited Company , http://www.gdledlight.com